W laboratoriach na całym świecie, destylator laboratoryjny stanowi kluczowe narzędzie do przeprowadzania różnorodnych badań i…
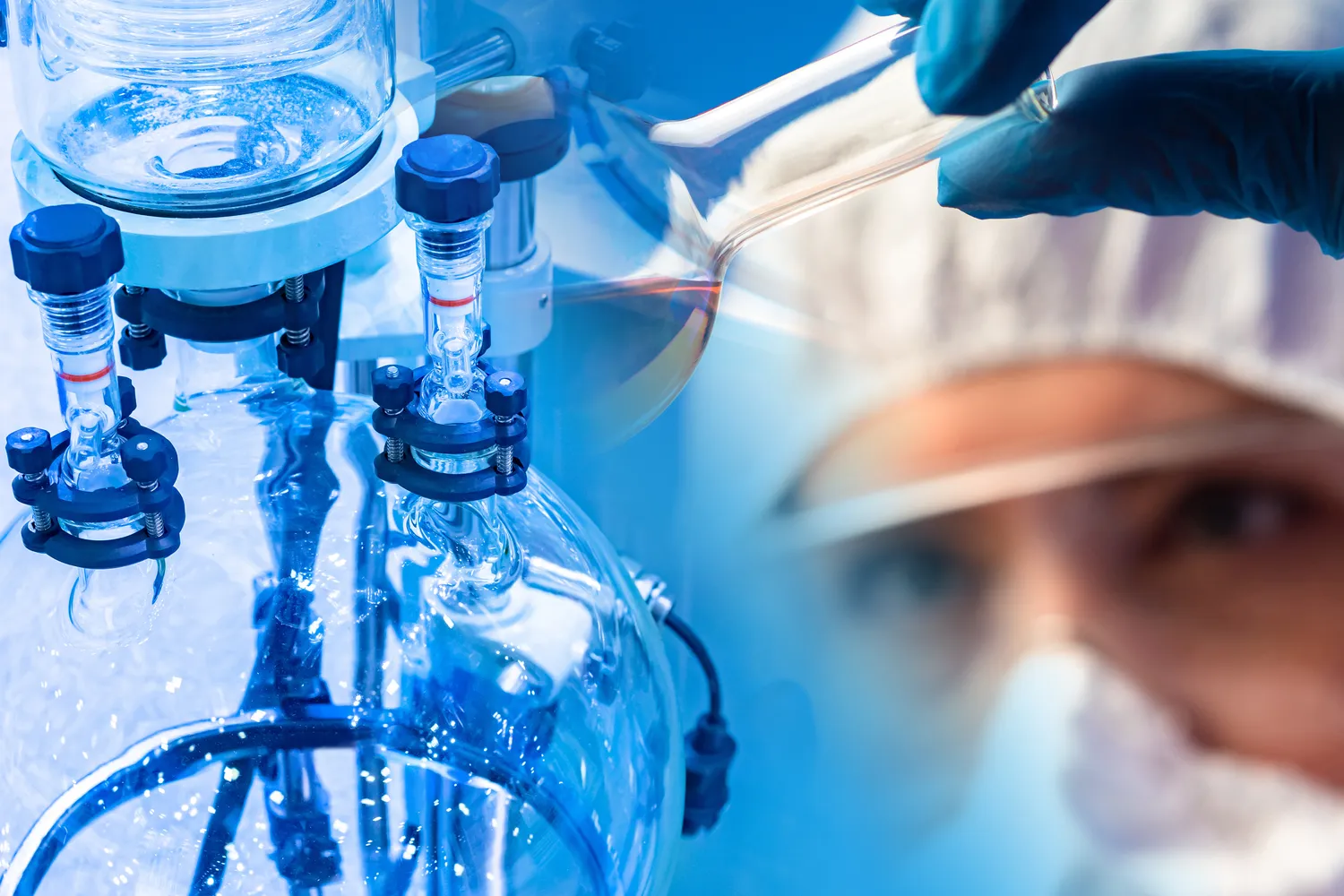
Destylator przemysłowy
Destylator przemysłowy to urządzenie wykorzystywane w różnych branżach do separacji cieczy na podstawie różnic w ich temperaturze wrzenia. Proces destylacji polega na podgrzewaniu mieszaniny, co prowadzi do odparowania składników o niższej temperaturze wrzenia, a następnie skraplaniu ich z powrotem w postaci cieczy. W przemyśle chemicznym, petrochemicznym oraz spożywczym destylatory odgrywają kluczową rolę w produkcji czystych substancji, takich jak alkohole, oleje czy rozpuszczalniki. W zależności od zastosowania, destylatory mogą mieć różne konstrukcje, od prostych kolumn po zaawansowane systemy z wieloma etapami separacji. W przemyśle chemicznym często stosuje się destylację frakcyjną, która pozwala na oddzielenie wielu składników jednocześnie.
Jakie są rodzaje destylatorów przemysłowych i ich zastosowanie
W przemyśle istnieje wiele rodzajów destylatorów, które różnią się konstrukcją oraz zastosowaniem. Jednym z najpopularniejszych typów jest destylator prosty, który składa się z naczynia grzewczego oraz chłodnicy. Tego rodzaju urządzenia są często wykorzystywane do produkcji alkoholu etylowego oraz innych rozpuszczalników. Kolejnym typem jest destylator frakcyjny, który umożliwia oddzielanie składników o zbliżonych temperaturach wrzenia. Dzięki zastosowaniu kolumny frakcyjnej możliwe jest uzyskanie wyższej czystości produktów końcowych. W przemyśle naftowym stosuje się również destylatory próżniowe, które działają w obniżonym ciśnieniu, co pozwala na destylację substancji w niższych temperaturach i minimalizuje ryzyko degradacji termicznej. Oprócz tego istnieją także destylatory azeotropowe, które są wykorzystywane do separacji mieszanin tworzących azeotropy.
Jakie są kluczowe zalety stosowania destylatorów przemysłowych
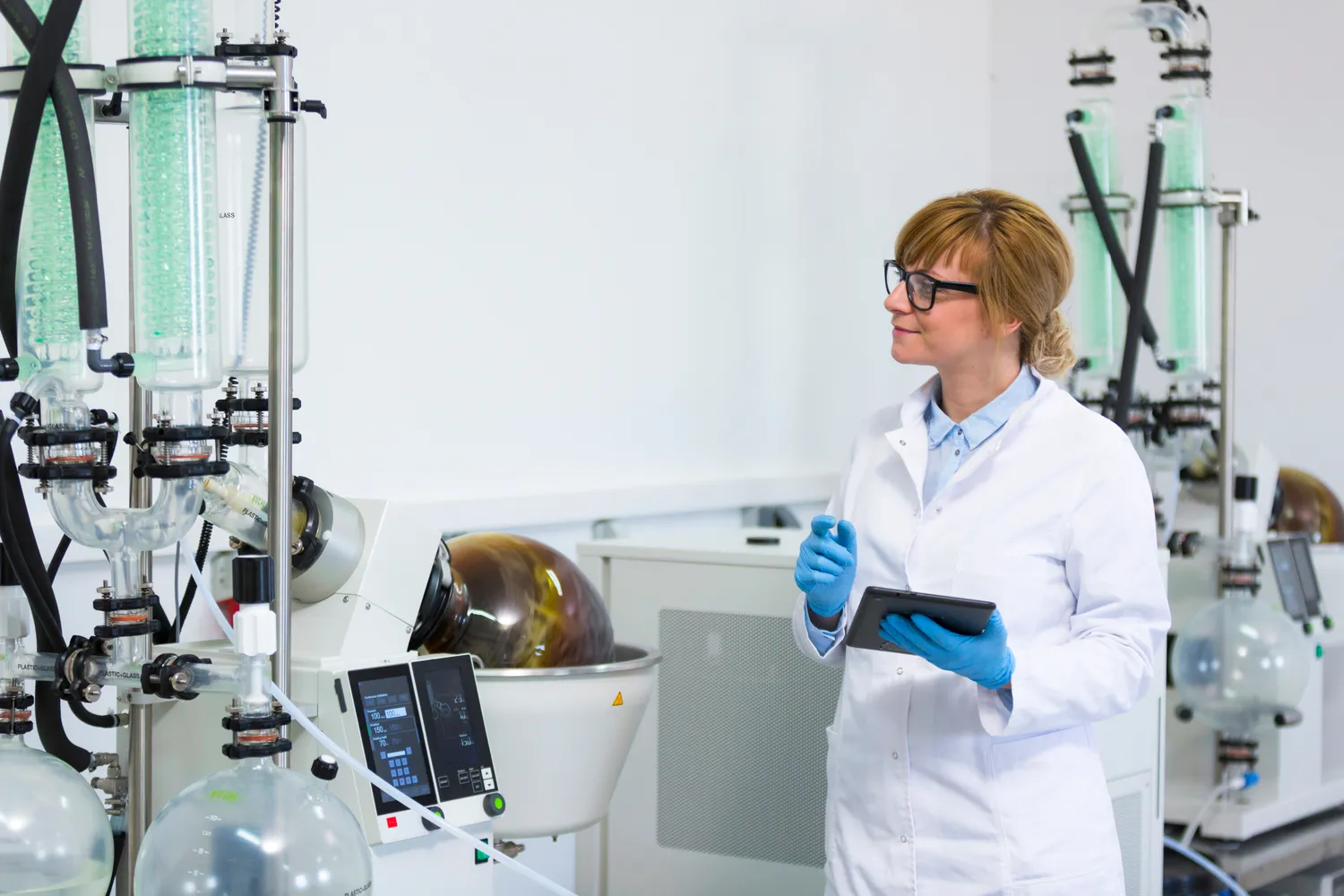
Stosowanie destylatorów przemysłowych niesie ze sobą wiele korzyści, które przyczyniają się do zwiększenia efektywności procesów produkcyjnych. Przede wszystkim pozwalają one na uzyskanie wysokiej czystości produktów końcowych, co jest istotne w branżach takich jak farmaceutyka czy chemia. Dzięki zastosowaniu nowoczesnych technologii i automatyzacji procesów możliwe jest osiągnięcie dużej wydajności oraz oszczędności energetycznych. Destylatory przemysłowe są również elastyczne i mogą być dostosowane do różnych rodzajów surowców oraz wymagań produkcyjnych. Kolejną zaletą jest możliwość ciągłej pracy tych urządzeń, co pozwala na optymalizację procesów i redukcję kosztów operacyjnych. Dodatkowo nowoczesne systemy monitorowania i kontroli jakości umożliwiają bieżące śledzenie parametrów procesu, co zwiększa bezpieczeństwo i niezawodność operacji.
Jakie są najczęstsze problemy związane z użytkowaniem destylatorów przemysłowych
Mimo licznych zalet użytkowanie destylatorów przemysłowych może wiązać się z pewnymi problemami technicznymi oraz operacyjnymi. Jednym z najczęstszych wyzwań jest utrzymanie odpowiednich warunków pracy urządzenia, takich jak temperatura czy ciśnienie. Niewłaściwe ustawienia mogą prowadzić do obniżenia wydajności procesu lub nawet uszkodzenia sprzętu. Ponadto regularne czyszczenie i konserwacja są kluczowe dla zachowania sprawności destylatora – osady mogą wpływać na jakość produktu końcowego oraz zwiększać zużycie energii. Innym istotnym problemem jest kontrola jakości surowców wejściowych; niejednorodność materiału może prowadzić do trudności w osiągnięciu pożądanych parametrów produktu końcowego. Również zmiany w składzie chemicznym surowców mogą wymagać dostosowania ustawień procesu lub nawet modyfikacji samego urządzenia.
Jakie są najnowsze technologie w destylacji przemysłowej
W ostatnich latach w dziedzinie destylacji przemysłowej pojawiły się liczne innowacje technologiczne, które znacząco poprawiły efektywność i jakość procesów. Jednym z najważniejszych trendów jest automatyzacja procesów destylacyjnych, która pozwala na zdalne monitorowanie i kontrolowanie parametrów pracy urządzeń. Dzięki zastosowaniu zaawansowanych systemów informatycznych oraz czujników możliwe jest bieżące dostosowywanie warunków pracy do zmieniających się potrzeb produkcyjnych. Kolejnym istotnym osiągnięciem są nowoczesne materiały konstrukcyjne, które charakteryzują się lepszą odpornością na korozję oraz wysoką temperaturę, co wydłuża żywotność destylatorów. Warto również zwrócić uwagę na rozwój technologii membranowych, które mogą stanowić alternatywę dla tradycyjnej destylacji, oferując mniejsze zużycie energii oraz lepszą selektywność separacji.
Jakie są wymagania dotyczące bezpieczeństwa w użytkowaniu destylatorów
Bezpieczeństwo podczas użytkowania destylatorów przemysłowych jest kluczowym aspektem, który należy uwzględnić na każdym etapie procesu produkcyjnego. Przede wszystkim operatorzy powinni być odpowiednio przeszkoleni w zakresie obsługi urządzeń oraz znajomości procedur awaryjnych. Właściwe oznakowanie stref zagrożonych oraz dostęp do sprzętu ochronnego, takiego jak rękawice czy okulary ochronne, są niezbędne dla zapewnienia bezpieczeństwa pracy. Ważnym elementem jest także regularna konserwacja i inspekcja urządzeń, co pozwala na wczesne wykrywanie potencjalnych usterek. Należy również zwrócić uwagę na systemy wentylacyjne, które powinny być odpowiednio zaprojektowane, aby minimalizować ryzyko gromadzenia się szkodliwych oparów. Dodatkowo warto implementować systemy detekcji gazów oraz alarmy przeciwwybuchowe, które mogą znacznie zwiększyć poziom bezpieczeństwa w zakładzie.
Jakie są koszty związane z zakupem i eksploatacją destylatora
Koszty związane z zakupem i eksploatacją destylatora przemysłowego mogą być znaczące i różnią się w zależności od wielu czynników, takich jak typ urządzenia, jego wydajność oraz zastosowane technologie. Koszt zakupu nowego destylatora może wynosić od kilku tysięcy do nawet milionów złotych w przypadku zaawansowanych systemów frakcyjnych czy próżniowych. Oprócz samego zakupu należy uwzględnić także koszty instalacji oraz uruchomienia urządzenia, które mogą być znaczące w przypadku skomplikowanych systemów. W trakcie eksploatacji należy brać pod uwagę koszty energii elektrycznej, która jest kluczowa dla procesu podgrzewania cieczy oraz chłodzenia pary. Koszty surowców wejściowych również mają istotny wpływ na całkowity koszt produkcji. Dodatkowo regularne przeglądy techniczne oraz konserwacja urządzenia generują dodatkowe wydatki, które należy uwzględnić w budżecie operacyjnym zakładu.
Jakie są perspektywy rozwoju branży destylacyjnej
Branża destylacyjna stoi przed wieloma wyzwaniami i możliwościami rozwoju w nadchodzących latach. W miarę rosnącego zapotrzebowania na czyste substancje chemiczne oraz biopaliwa następuje wzrost inwestycji w nowoczesne technologie destylacyjne. Przemiany związane z ekologią i zrównoważonym rozwojem skłaniają producentów do poszukiwania bardziej efektywnych i ekologicznych metod separacji substancji chemicznych. Wprowadzenie innowacyjnych technologii, takich jak destylacja membranowa czy wykorzystanie energii słonecznej do podgrzewania cieczy, może przyczynić się do znacznego obniżenia kosztów operacyjnych oraz zmniejszenia wpływu na środowisko naturalne. Również rozwój cyfryzacji i automatyzacji procesów produkcyjnych otwiera nowe możliwości optymalizacji pracy destylatorów oraz zwiększenia ich wydajności. Warto zauważyć, że zmiany regulacyjne dotyczące ochrony środowiska mogą wpłynąć na sposób funkcjonowania branży, co wymusi dostosowanie się do nowych norm i standardów jakościowych.
Jakie są różnice między destylacją a innymi metodami separacji
Destylacja to jedna z wielu metod separacji substancji chemicznych, jednak różni się ona od innych technik pod względem zasad działania oraz zastosowań. Główną różnicą między destylacją a ekstrakcją jest to, że ekstrakcja polega na rozpuszczaniu jednego składnika w rozpuszczalniku, podczas gdy destylacja opiera się na różnicach temperatur wrzenia składników mieszaniny. Inną popularną metodą separacji jest filtracja, która polega na oddzieleniu ciał stałych od cieczy lub gazu za pomocą materiału filtracyjnego; jednak filtracja nie jest skuteczna w przypadku mieszanin ciekłych zawierających substancje o podobnej wielkości cząsteczkowej. Chromatografia to kolejna technika separacyjna stosowana głównie w laboratoriach analitycznych; jej zasada opiera się na różnicach w powinowactwie składników do fazy stacjonarnej i ruchomej.
Jakie są najczęstsze błędy przy obsłudze destylatorów przemysłowych
Obsługa destylatorów przemysłowych wymaga dużej precyzji oraz znajomości zasad działania urządzeń; jednak wiele osób popełnia błędy, które mogą prowadzić do obniżenia efektywności procesu lub uszkodzenia sprzętu. Jednym z najczęstszych błędów jest niewłaściwe ustawienie parametrów pracy urządzenia, takich jak temperatura czy ciśnienie; brak ich optymalizacji może prowadzić do nieefektywnej separacji składników lub nawet ich degradacji termicznej. Kolejnym problemem jest zaniedbanie regularnej konserwacji i czyszczenia sprzętu; osady mogą wpływać na jakość produktu końcowego oraz zwiększać zużycie energii. Niezrozumienie charakterystyki surowców wejściowych również może prowadzić do trudności w osiągnięciu pożądanych rezultatów – zmiany w składzie chemicznym surowców wymagają dostosowania procesu produkcyjnego.