Mechanika oraz budowa maszyn to dziedziny inżynierii, które odgrywają kluczową rolę w projektowaniu, analizie oraz…
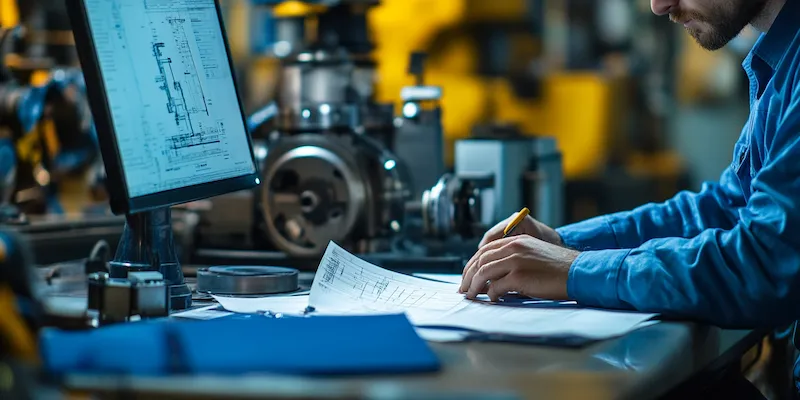
Budowa maszyn roboczych
Budowa maszyn roboczych to złożony proces, który wymaga uwzględnienia wielu kluczowych elementów. W każdej maszynie roboczej można wyróżnić kilka podstawowych komponentów, które odpowiadają za jej funkcjonalność i wydajność. Do najważniejszych z nich należy zaliczyć układ napędowy, który jest odpowiedzialny za przekazywanie mocy do poszczególnych części maszyny. W skład układu napędowego wchodzą silniki, przekładnie oraz systemy hydrauliczne lub pneumatyczne, które umożliwiają ruch i działanie maszyny. Kolejnym istotnym elementem jest konstrukcja nośna, która zapewnia stabilność i wytrzymałość całej maszyny. W zależności od przeznaczenia maszyny, konstrukcja ta może być wykonana z różnych materiałów, takich jak stal czy aluminium. Nie można zapomnieć o systemach sterowania, które pozwalają na precyzyjne zarządzanie pracą maszyny.
Jakie technologie są wykorzystywane w budowie maszyn roboczych
W budowie maszyn roboczych wykorzystuje się szereg nowoczesnych technologii, które mają na celu zwiększenie ich wydajności oraz funkcjonalności. Jedną z kluczowych innowacji jest zastosowanie technologii CAD (Computer-Aided Design), która umożliwia projektowanie skomplikowanych struktur maszyn w trójwymiarze. Dzięki temu inżynierowie mogą dokładnie zweryfikować wszystkie aspekty konstrukcji przed rozpoczęciem produkcji. Kolejną istotną technologią jest CAM (Computer-Aided Manufacturing), która wspiera procesy produkcyjne poprzez automatyzację obróbki materiałów. W kontekście budowy maszyn roboczych coraz większą rolę odgrywa również technologia 3D printing, która pozwala na szybkie prototypowanie oraz produkcję skomplikowanych części bez konieczności użycia tradycyjnych narzędzi. Warto także zwrócić uwagę na rozwój systemów monitorowania i diagnostyki maszyn, które pozwalają na bieżąco kontrolować ich stan techniczny oraz przewidywać potencjalne awarie.
Jakie są najpopularniejsze rodzaje maszyn roboczych
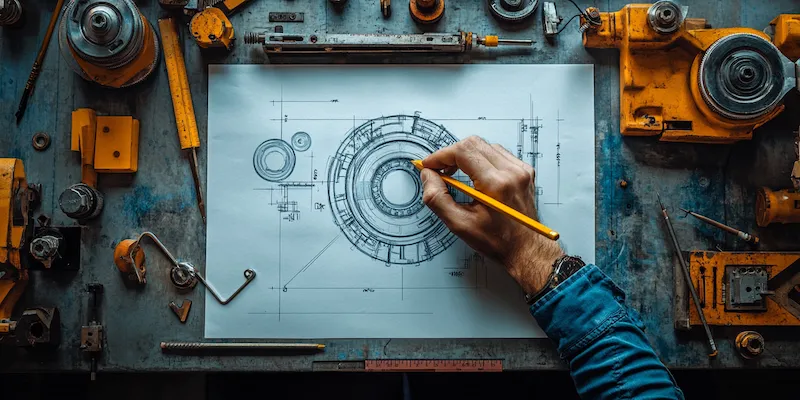
Na rynku dostępnych jest wiele różnych rodzajów maszyn roboczych, które znajdują zastosowanie w różnych branżach przemysłowych. Jednym z najpopularniejszych typów są maszyny budowlane, takie jak koparki, ładowarki czy dźwigi, które służą do wykonywania prac ziemnych oraz transportu materiałów. W przemyśle ciężkim często spotykane są maszyny do obróbki metali, takie jak tokarki czy frezarki, które umożliwiają precyzyjne formowanie i kształtowanie materiałów. W sektorze rolniczym dominują maszyny rolnicze, takie jak ciągniki czy kombajny, które ułatwiają prace związane z uprawą roli oraz zbiorami plonów. W ostatnich latach coraz większą popularnością cieszą się również maszyny automatyczne i roboty przemysłowe, które są wykorzystywane do zautomatyzowanej produkcji w fabrykach. Te nowoczesne rozwiązania przyczyniają się do zwiększenia wydajności oraz redukcji kosztów pracy.
Jakie są najczęstsze problemy w budowie maszyn roboczych
Budowa maszyn roboczych wiąże się z wieloma wyzwaniami i problemami, które mogą wpłynąć na jakość końcowego produktu oraz jego funkcjonalność. Jednym z najczęstszych problemów jest niewłaściwe dobranie materiałów do konstrukcji maszyny. Użycie niewłaściwych surowców może prowadzić do osłabienia struktury oraz skrócenia żywotności urządzenia. Kolejnym istotnym zagadnieniem jest błędne zaprojektowanie układów mechanicznych lub elektronicznych, co może skutkować awariami podczas eksploatacji. Problemy te często wynikają z braku doświadczenia projektantów lub niedostatecznej analizy wymagań użytkowników końcowych. Dodatkowo proces produkcji samych komponentów może być źródłem problemów; niewłaściwe tolerancje czy błędy w obróbce mogą prowadzić do trudności w montażu i późniejszym użytkowaniu maszyny. Ważnym aspektem jest również zapewnienie odpowiednich warunków testowych przed oddaniem maszyny do użytku; brak rzetelnych testów może prowadzić do nieprzewidzianych usterek w trakcie pracy urządzenia.
Jakie są kluczowe etapy w procesie budowy maszyn roboczych
Proces budowy maszyn roboczych składa się z kilku kluczowych etapów, które są niezbędne do osiągnięcia finalnego produktu o wysokiej jakości. Pierwszym krokiem jest faza projektowania, w której inżynierowie opracowują koncepcję maszyny oraz jej poszczególnych komponentów. W tym etapie ważne jest uwzględnienie specyfikacji technicznych, wymagań użytkowników oraz norm bezpieczeństwa. Po zakończeniu etapu projektowania następuje faza prototypowania, w której tworzy się pierwszy model maszyny. Prototyp pozwala na przetestowanie wszystkich rozwiązań konstrukcyjnych oraz identyfikację ewentualnych problemów przed rozpoczęciem produkcji seryjnej. Kolejnym etapem jest produkcja komponentów, która obejmuje obróbkę materiałów oraz montaż poszczególnych części maszyny. W tym czasie niezwykle istotne jest zapewnienie odpowiedniej jakości wykonania, aby uniknąć późniejszych usterek. Po zmontowaniu maszyny przeprowadza się szereg testów funkcjonalnych, które mają na celu sprawdzenie jej wydajności oraz bezpieczeństwa.
Jakie są najważniejsze normy i przepisy dotyczące budowy maszyn roboczych
Budowa maszyn roboczych podlega wielu normom i przepisom, które mają na celu zapewnienie bezpieczeństwa ich użytkowania oraz ochrony środowiska. W Europie kluczowym dokumentem regulującym te kwestie jest dyrektywa maszynowa 2006/42/WE, która określa wymagania dotyczące konstrukcji i eksploatacji maszyn. Zgodnie z tą dyrektywą, każda maszyna musi być zaprojektowana i wykonana w taki sposób, aby minimalizować ryzyko wystąpienia zagrożeń dla zdrowia i życia ludzi oraz dla środowiska naturalnego. W ramach tej dyrektywy producent zobowiązany jest do przeprowadzenia oceny ryzyka oraz sporządzenia dokumentacji technicznej, która potwierdza zgodność maszyny z wymaganiami prawnymi. Dodatkowo istnieją różne normy europejskie, takie jak EN ISO 12100 dotycząca ogólnych zasad projektowania maszyn czy EN 60204-1 dotycząca bezpieczeństwa elektrycznego maszyn. Przestrzeganie tych norm jest kluczowe nie tylko dla zapewnienia bezpieczeństwa użytkowników, ale także dla uzyskania odpowiednich certyfikatów, które umożliwiają wprowadzenie maszyny na rynek europejski.
Jakie są przyszłościowe kierunki rozwoju budowy maszyn roboczych
Przyszłość budowy maszyn roboczych zapowiada się niezwykle interesująco dzięki dynamicznemu rozwojowi technologii oraz rosnącym wymaganiom rynku. Jednym z najważniejszych kierunków rozwoju jest automatyzacja procesów produkcyjnych, która pozwala na zwiększenie wydajności oraz redukcję kosztów pracy. Wprowadzenie robotów przemysłowych do linii produkcyjnych staje się standardem w wielu branżach, co wpływa na zmiany w projektowaniu maszyn roboczych. Kolejnym istotnym trendem jest rozwój inteligentnych systemów sterowania opartych na sztucznej inteligencji i uczeniu maszynowym. Dzięki tym technologiom maszyny będą mogły samodzielnie dostosowywać swoje parametry pracy do zmieniających się warunków otoczenia oraz optymalizować swoje działanie w czasie rzeczywistym. Warto również zwrócić uwagę na rosnącą popularność zrównoważonego rozwoju i ekologicznych rozwiązań w budowie maszyn roboczych. Producenci coraz częściej poszukują materiałów przyjaznych dla środowiska oraz wdrażają technologie zmniejszające emisję szkodliwych substancji podczas produkcji i eksploatacji maszyn.
Jakie umiejętności są potrzebne do pracy w budowie maszyn roboczych
Praca w dziedzinie budowy maszyn roboczych wymaga szerokiego wachlarza umiejętności i kompetencji technicznych. Kluczową rolę odgrywa znajomość zasad mechaniki oraz inżynierii materiałowej, co pozwala na właściwe projektowanie i dobór komponentów do konstrukcji maszyny. Osoby pracujące w tej branży powinny również posiadać umiejętności związane z obsługą programów CAD/CAM, które są niezbędne do tworzenia projektów oraz planowania procesów produkcyjnych. Wiedza z zakresu automatyki i elektroniki staje się coraz bardziej istotna ze względu na rosnącą automatyzację procesów oraz zastosowanie zaawansowanych systemów sterowania w nowoczesnych maszynach roboczych. Umiejętność analizy danych oraz znajomość metod diagnostyki technicznej również są niezbędne do skutecznego monitorowania stanu technicznego urządzeń i przewidywania potencjalnych awarii. Ważnym aspektem jest także umiejętność pracy zespołowej oraz komunikacji między różnymi działami firmy, co pozwala na efektywne zarządzanie projektami budowy maszyn.
Jakie są zalety korzystania z nowoczesnych maszyn roboczych
Korzystanie z nowoczesnych maszyn roboczych przynosi wiele korzyści zarówno dla przedsiębiorstw, jak i dla pracowników wykonujących różnorodne zadania przemysłowe. Przede wszystkim nowoczesne maszyny charakteryzują się wyższą wydajnością i precyzją działania niż ich starsze odpowiedniki, co przekłada się na lepszą jakość produktów końcowych oraz szybsze tempo realizacji zamówień. Dzięki zastosowaniu zaawansowanych technologii automatyzacji możliwe jest znaczne ograniczenie błędów ludzkich podczas produkcji, co wpływa na poprawę efektywności operacyjnej firmy. Nowoczesne maszyny często wyposażone są w systemy monitorowania stanu technicznego oraz diagnostyki, co pozwala na bieżąco kontrolować ich wydajność i przewidywać awarie zanim do nich dojdzie; to z kolei prowadzi do zmniejszenia kosztów utrzymania sprzętu i przestojów produkcyjnych. Dodatkowo nowoczesne rozwiązania często uwzględniają aspekty ergonomiczne, co zwiększa komfort pracy operatorów i przyczynia się do poprawy ich bezpieczeństwa podczas wykonywania obowiązków zawodowych.
Jakie są wyzwania związane z konserwacją maszyn roboczych
Konserwacja maszyn roboczych to kluczowy aspekt ich eksploatacji, który wiąże się z wieloma wyzwaniami zarówno dla właścicieli firm, jak i dla personelu odpowiedzialnego za utrzymanie sprzętu w dobrym stanie technicznym. Jednym z głównych wyzwań jest konieczność regularnego przeprowadzania przeglądów technicznych oraz konserwacji zgodnie z zaleceniami producenta; zaniedbanie tego aspektu może prowadzić do poważnych awarii oraz skrócenia żywotności maszyny. Kolejnym problemem jest dostępność odpowiednich części zamiennych; w przypadku starszych modeli może być trudno znaleźć oryginalne komponenty, co może wpłynąć na czas naprawy i koszty związane z utrzymaniem sprzętu. Dodatkowo wiele nowoczesnych maszyn wykorzystuje zaawansowane technologie elektroniczne i automatyczne systemy sterowania, co wymaga od personelu specjalistycznej wiedzy i umiejętności związanych z diagnostyką i naprawą tych systemów.